氢燃料电池车(Fuel cell vehicle-FCEV)是使氢或含氢物质及空气中的氧通过燃料电池以产生电力,再以电力推动电动机,由电动机推动车辆,整个过程将氢的化学能转换为机械能。氢能源的最大好处是跟空气中的氧反应产生水蒸气之后排出,可有效减少燃油汽车造成的空气污染问题,现阶段下高速车辆、巴士、潜水艇和火箭已经在不同形式使用氢燃料,而燃料电池车一般在内燃机的基础上改良而成。目前燃料电池行业无论从技术储备还是商业模式仍处于积极探索中,技术上(电堆和整车技术)的可靠性和经济性都是制约燃料电池行业发展的瓶颈。当前影响国内加氢站终端氢气售价的主要因素是氢气到站成本(占70%),其中包括氢气成本和储氢、运氢成本。因此除降低储氢和运氢成本之外,如何获得低成本的氢源,将是实现终端加氢站运营经济性的关键。
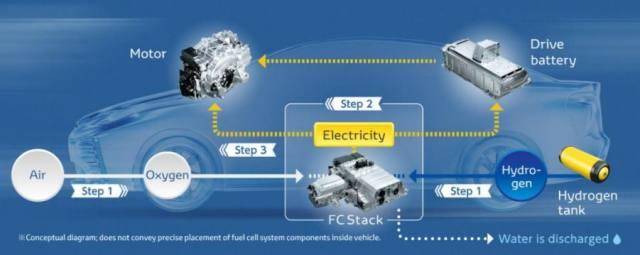
燃料电池驱动车辆的原理
目前国内用于外供氢气的氢能储备非常充足,但目前下游供氢体系尚处于萌芽探索阶段,几种制氢路线的经济性尚处验证之中。展望未来,由于负荷中心的集中区域华东地区煤炭总量指标控制严格,且中期内天然气供给仍将较为紧张,投资较重的化石燃料制氢(煤制氢和天然气重整制氢)作为定向的供氢路线,其可行性获得确认之前难以大规模推广;而水电解路线虽然可以实现分散式供氢,但其经济性取决于电力成本的降低,国内风电和光伏的弃电利用水平是制约该路线未来发展程度的关键。
从目前来看,国内化工副产氢的利用是燃料电池行业供氢的较优选择,国内氯碱、PDH 和快速发展的乙烷裂解行业可提供充足的低成本氢气资源,且集中在负荷中心密集的华东地区,在对这些装置进行低强度的改造之后可同时解决燃料电池行业的供氢和副产氢高效利用的问题,未来化工副产集中式供氢+水电解分散式制氢将会是国内燃料电池行业供氢模式的发展方向。

不同制氢路线的经济规模和制氢成本等的比较
(1)从出厂成本来看,焦炉气、氯碱、丙烷脱氢制丙烯和乙烷裂解制烯烃副产的粗氢气可以经过脱硫、变压吸附和深冷分离等精制工序后作为燃料电池车用氢源,成本远低于化工燃料制氢、甲醇重整制氢和水电解制氢等路线。
(2)从副产的氢气量来看,国内焦化行业产能巨大,可副产氢气量较大,但由于焦化产能集中在山西、河北和山东等华北地区,距离长三角等负荷中心较远,且分离精制成本较高,而考虑到储氢和运氢后的综合成本与氯碱、丙烷脱氢和乙烷裂解制氢相比更是不占优势。
(3)综合来看,现有的 PDH 产能约 588 万吨,考虑在建和前期准备中的产能,未来国内将合计拥有 915 万吨产能,可副产并外售 30.5 万吨氢气,可以满足约 213 万辆燃料电池车用氢量;而规划中的乙烷裂解产能达 1460 万吨,可以实现的外供氢气量达 93.4 万吨,规模更为巨大,可满足约 653 万辆燃料电池车用氢需求。此外丙烷脱氢和乙烷裂解装置基本上集中在沿海港口地区,通过进一步的低投资强度的精制工序,氢气中的总硫、CO 等杂质含量便可符合燃料电池用氢气标准,因此丙烷脱氢和乙烷裂解副产的氢气将是未来潜在最具优势的燃料电池车用氢源选择之一。

沿海氢源走廊
目前工业上生产氢气的技术已经非常成熟,化石燃料制氢、化工副产氢、水电解制氢、甲醇制氢各种路线均已经大规模商业应用,此外光电化学和生物制氢尚处于技术开发阶段。而从国内外加氢站的运营情况来看,目前供氢的方式主要分为两种:站内制氢和外供氢气。其中站内制氢主要是水电解制氢,该技术已经相当成熟并且在欧洲大多数加氢站获得应用;而外供氢气则是大规模的利用天然气重整制氢或者钢厂、化工厂副产氢气,在净化之后使用高压氧气瓶集束拖车运输至加氢站。

氢能体系的组成
目前电堆和整车技术的可靠性和经济性都是制约燃料电池行业发展的瓶颈,除了降低储氢和运氢成本之外,如何获得低成本的氢源,将是实现终端加氢站运营经济性的关键。
从目前来看国内化工副产氢的利用是燃料电池行业供氢的较优选择,市场普遍认为国内氯碱厂提供的低成本氢气资源是国内燃料电池行业氢源的最优选择。与市场的普遍认知不同,氢云链认为随着北美页岩油气革命之后国内碳三和碳二行业生产路线发生了变革性的变化:考虑在建和规划中的产能,未来国内PDH(丙烷脱氢)产能将达 915 万吨产能,而规划中的乙烷裂解产能达 1460 万吨。两者合计可副产外售 123.9 万吨氢气,可满足约 866 万辆燃料电池车用氢需求。PDH 和乙烷裂解集中在沿海港口地区,通过低强度的改造便可满足燃料电池用氢气,PDH 和乙烷裂解副产的氢气将是未来潜在最具优势的燃料电池车用氢源选择之一。