
本次标定是自装置开车后的第二次标定,是对装置长周期运行水平进行总体评价,主要考察装置实际运行水平和催化剂寿命,掌握技术参数、产品质量、能耗以及设备运行状况。在装置标定过程中,项目团队严格制定标定方案,精心操作巡检,严格按照安全标准程序作业,确保装置标定全面受控。专家组全程跟随记录,采集装置信息,实时分析考核装置运行情况。
现场考核和标定结果显示:工业装置连续稳定运行期间的反应压力10.1~10.5 MPa、钌催化剂热点温度432~440 ℃、钌催化剂床层出口温度423~430℃、出口氨浓度17.6~18.7%、氨净值14.51~15.58 v%,达到设计要求和预期目标。
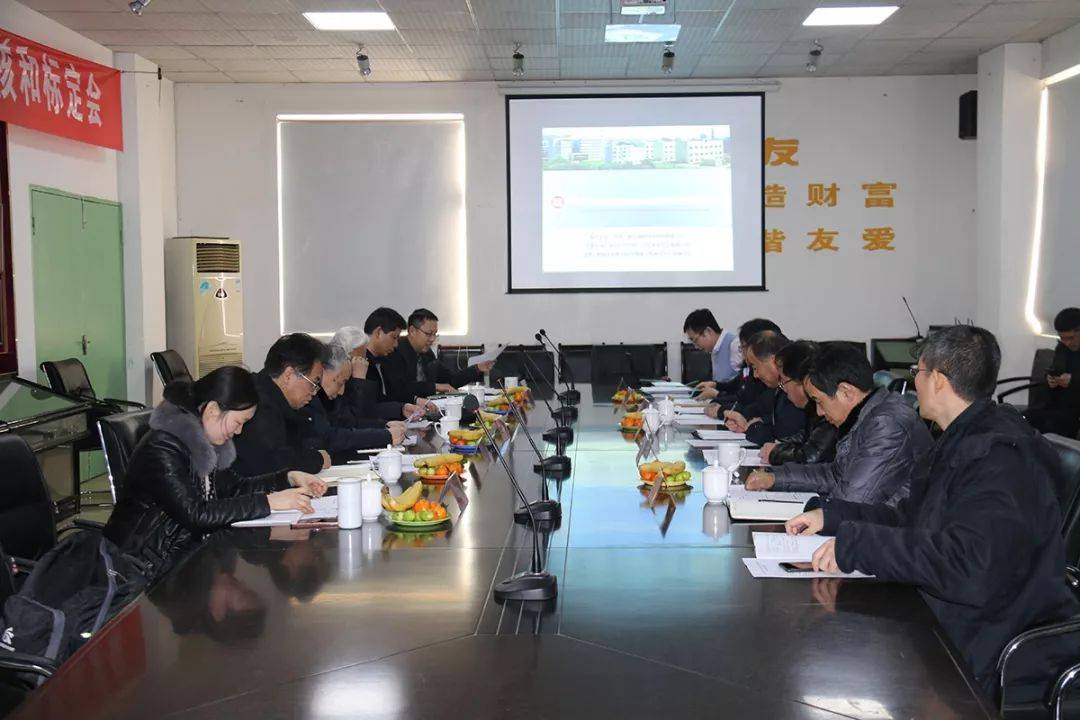
由中国工程院院士舒兴田、中国石油咨询中心高级工程师门存贵带领的考核专家组一致认为:“铁钌接力催化”低温低压合成氨工业装置反应压力平稳,钌催化剂床层及合成塔出口温度稳定,反应器出口氨浓度和氨净值稳定,钌系氨合成催化剂活性和稳定性高,成套技术、工艺及装置满足工业连续生产要求。该成套技术节能效果和经济效益显著,本质安全性进一步提高,社会和环境效益好,有利于合成氨工业升级换代。

去年3月,低温低压钌系合成氨工业示范装置通过了中国石油与化学工业联合会的72小时标定考核。标定专家组组长、中国工程院院士舒兴田对标定结果给予了高度评价。他表示:“传统的合成氨工业采用铁系催化剂反应压力高、温度高、能耗高,效率低。三聚环保与福州大学等多家单位组成的研发团队在高活性、高稳定性的钌系催化剂以及在铁钌连串催化成套技术上取得的突破,将支撑我国合成氨工业技术实现跨越式的进步。”
研发团队负责人、福州大学化肥催化剂国家工程研究中心主任江莉龙这项技术历经两代人20多年的艰苦努力研发成功,通过产学研深度融合,该技术在江苏禾友化工有限公司首次实现了万吨级工业示范,在降低生产成本和提高产量上显示出良好前景。以18万吨/年合成氨装置为例初步估算,该成套技术每年将为企业节省能耗支出3000多万元,提高产能33.6%以上,新增产值1亿多元。三聚环保