记者6月25日从国家电力投资集团有限公司科技成果发布会上海核工程研究设计院有限公司(以下简称“上海核工院”)专场了解到,在国和一号(CAP1400)开发过程中,已形成新产品、新材料、新工艺、新装置等392项,形成知识产权4699项,形成行业、企业标准近200项。这组数字的背后,是中国核电行业数年的磨砺。
“这其中的很多材料和装置原本都需要进口。通过重大专项的实施,这些产品和材料基本实现了国产化。对于我国可能出口核电的国家和地区,我们也相应申请了国外专利,确保将来走得出去。”国家科技重大专项“大型先进压水堆核电站”总设计师、上海核工程研究设计院院长郑明光在发布会上表示,国和一号/CAP1400的自主设计和开发带动了国内制造业体系的跃升。
一个国家的核电实力强不强,首先要看有没有自主设计能力。若不具备自主设计能力,只能是盘桓在中低端水平的翻版或触及侵权红线。核电站属于安全标准极高、系统复杂且精密的超级工程,自主型号研制不可能是一路坦途。郑明光此前接受专访时曾回忆说,核电安全标准的大大提高,对整个设备的可靠性设计、系统的可靠性设计都是极大的考验。再加上,彼时中国的装备制造业尚难以满足国和一号/CAP1400的要求,围绕型号的创新目标,设计方与制造方需要“跳一跳才够得着”。
回顾10年前,参照三代核电的设计规格书,国内没有一家装备企业能完整有效地制造出三代核电设备,通过引进三代核电AP1000自主化依托项目、国和一号/CAP1400重大专项及其他三代核电项目的拉动,国内培育出全产业链的三代核电设备供应能力,中国核电装备实现了从二代到三代的重大跨越。反过来,得益于关键设备国产化、大容量和简化系统、模块化建造等特点,当前世界最大的非能动压水堆核电站国和一号/CAP1400的经济性格外突显,肩负着中国核电技术出海、带动中国核电装备“走出去”的使命。
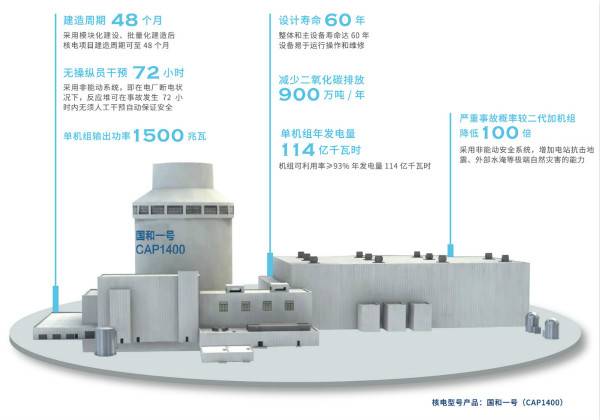
重大专项培育核电关键设备国产化
郑明光在发布会上介绍称,国和一号/CAP1400的开发属于“高起点再创新”,它基于中国50年的核电厂研发、设计和工程经验,基于中国44个机组20多年的安全建设和运行经验,基于AP1000技术的消化吸收,也基于AP1000依托项目的建设经验。
2006年11月,国家决定引进美国西屋公司AP1000技术。浙江三门核电站和山东海阳核电站共4台机组被确定为中国三代核电自主化依托项目,2009年开始相继开工,并于2018年底、2019年初相继并网发电。
2008年2月15日,国务院常务会议正式通过压水堆重大专项总体实施方案,并将CAP1400的研发和示范工程建设列为重大专项的重点任务,由AP1000的技术受让方国家
核电技术公司牵头,实行产学研结合,广泛吸收有关单位共同攻关。
基于AP1000技术,CAP1400型号在确定之初就被定位为:安全性不低于AP1000、经济性好于AP1000,整体设计寿命60年。其中,“C”为“中国”英文单词的首字母,“A”、“P”分别代表“先进(Advanced)”和“非能动(Passive)”英文单词的首字母,CAP1400的含义即为中国装机容量为140万千瓦的先进非能动核电技术,2018年这一型号的中文名被确定为“国和一号”。国和一号/CAP1400采用非能动安全系统,机组设计寿命60年,换料周期18个月,机组可利用率约93%,满足目前世界上最严格的安全标准。
面对西屋公司提出的“135万千瓦自主知识产权净功率红线”,中方设计团队唯有对国和一号/CAP1400进行革命性的、更大幅度的创新。通过扩大安全壳直径、增加蒸汽发生器流通面积等一系列根本性创新,国和一号/CAP1400的设计较AP1000开辟了另一片新天地:比如,采用反应堆系统性低压损设计,流量增加了21%,扬程降低5%;堆芯方案从AP1000的157盒燃料组件变成了193盒燃料组件;蒸汽发生器提高传热效率,自主设计了汽水分离装置和新型蒸汽限流器;反应堆压力容器减少了焊缝;堆内构件取消了中子屏蔽板和流量分配裙,增加了吊篮刚度等等。

在顶层设计革新的基础上,新的核电型号离不开新设备的支撑。三代核电更高的安全标准要求、技术标准要求、技术参数要求对国内设备厂商的软硬件能力提出了新的挑战,当时国产化设备的制造能力还未达到能制造如此大功率设备的水平。“2007年、2008年,当时我们以三代核电的设计规格书请制造企业生产设备,当时国内没有一家企业能完整有效地制造出三代核电设备。”郑明光回忆道。在此番时境下,一场设计方与设备方形成创新联合体进行技术攻关的长跑随之启动。
在发布会上,上海核工院工程设备所副所长矫明分享了几个三代核电关键设备和材料的国产化案例。核岛关键设备价格往往高达几千万到数亿元不等,重达几百吨接近上千吨,对设计制造能力及制造商对于设计图纸的理解能力的要求都非常高。
反应堆压力容器是承载反应堆的核心设备、要求60年不可更换,设计寿命要求非常高。减少主环路的焊缝,可以大大提高核电技术安全性并减少运维时间,因此,国和一号/CAP1400创新性地采用了整体锻造顶封头管嘴和一体化底封头。相比于堆焊,一体化焊件对制造厂装备配套能力的要求又上了一个台阶。
功能类似于高压锅密封圈的反应堆压力容器O型密封环,曾几何时是国外采购经常被禁运的设备。“密封”是核电运行和事故状态下防止泄漏的第一关,这种零部件对庞大的核电站来说看似微小,但曾是真正的“卡脖子”环节,O型密封环更是整个核电密封系统中最复杂、最重要的密封,从国外购买的价格高达几百万。该设备的国产化是国和一号/CAP1400研究开发过程中一个急需突破的难题。为此,上海核工院和和宁波天生密封件有限公司联合成立了核电密封联合研究中心,经过多年研制打破了国外垄断,国产化后产品价格约为三四十万元。
类似的由工程需求牵引出设备技术需求、设计方提出研制方案,设计方与制造方联合攻克的关键设备和材料还包括大型铸锻件、蒸发器690合金传热管、焊接材料等等。为降低设备研制风险并培育良性的竞争氛围,国和一号/CAP1400在开展设备研制及国产化过程中,对蒸汽发生器、压力容器、主泵、主管道等关键设备均安排2-3家厂家进行培育,目前设备的国产化率已超过85%,可进一步达到90%以上。其余10%是可以国际采购的通用设备,目前没有特别受制于人的物项。
在国和一号/CAP1400等三代核电技术的带动下,国内各大制造企业完成了从不会到会、装备制造能力从二代核电到三代核电的跃升,这同时支撑了如先进小堆等国内核电型号的开发。
当前,国内已具备年产10台套以上的核电装备制造能力,位居全球第一。一位国内一线装备制造企业高管对澎湃新闻介绍,在这个过程中,中国企业的装备能力在一些机械加工设备和重要工具工装上已达到世界顶尖水平。中国装备制造业的软实力也得以提升,项目与技术管理也得以优化,人员队伍的能力素养得到了进一步历练。
做“减法”的简化设计,经济性富有竞争力
为保障核电机组的安全,国和一号/CAP1400在AP1000基础上进一步提升了安全裕量:采用了非能动安全系统,利用物质的储能、重力、对流、蒸发、冷凝等自然力,不依赖外部电源,能确保反应堆安全和余热导出,事故后操纵员可不干预时间从“二代加”核电技术的30分钟提高到72小时;堆芯损伤频率和大量放射性物质释放频率较美国核电用户要求文件限值低一个量级;具有系统性的严重事故预防和缓解措施;屏蔽厂房采用先进的钢板混凝土结构,具备抗大型商用飞机恶意撞击的能力等。
在此基础上,国和一号/CAP1400还充分落实了福岛事故后核安全的增强要求,包括提高纵深防御系统的抗震能力与电源可靠性,提高电厂抵御极端外部事件的能力,强化事故72小时后冷却水和电力的供应能力,强化电厂应对超设计基准事故的能力等等。
在保证高安全性的前提下,现如今核电作为电力商品的属性正在凸显,作为“电”的经济性,是决定核电在全球电力市场中竞争性的重要指标。据澎湃新闻了解,上海核工院曾经做过测算,国和一号/CAP1400批量化建造之后,倒推出的每千瓦时电价约为0.35至0.38元,颇具竞争力。
郑明光对澎湃新闻表示,国和一号/CAP1400经济性优于AP1000。一方面来源于机组效能、发电规模,另一方面是设备国产化之后具备更强的竞争力。因为设备的产业链是由多家制造企业构成,所以设备国产化、自主化后价格比引进设备便宜,同时促进了经济性的提高,这主要是来自于系统性能的增强,系统效率的提高,经济价格的合理。
最为核心的是,国和一号/CAP1400采用简化设计和模块化设计,用做“减法”的思路,把设备结构简单化,采用“非能动”原理,紧急情况下不需要使用交流电源,仅仅依靠重力、热循环和冷凝等自然手段作为动力排出余热。与二代核电相比,国和一号/CAP1400的阀门数量减少了80.4%、泵的数量减少92.3%、管道数量减少58.5%、电缆数量减少了48.6%,在提高经济性的同时,更便于运行和维护。同时,基于AP1000依托项目的经验反馈,国和一号/CAP1400进一步优化了模块化建造技术,批量化建造后核电项目的建造周期可至48个月,这大大少于目前国际主流核电机组工期。对于资金密集型核电产业而言,工期缩短的重要意义不言而喻。