在24日下午的“储能电站规划与设计”专场,深圳普瑞赛思检测技术有限公司电池测试资深工程师范亚飞分享了主题报告《储能电池的安全测评与灾害防控》。会务组对发言人的演讲速记做了梳理,方便大家会后交流、学习,以下是速记全文:
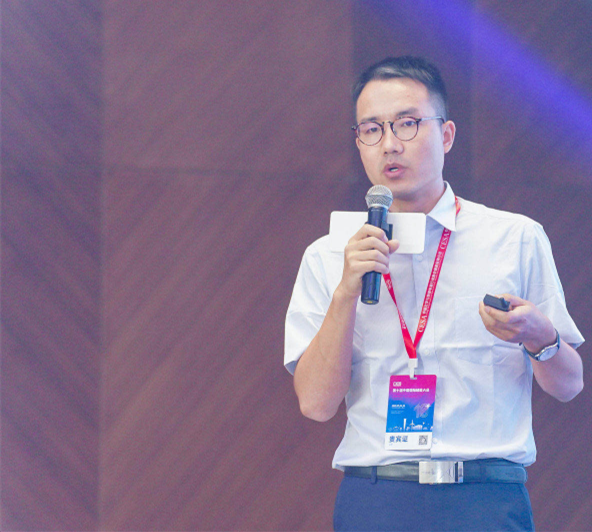
范亚飞:各位专家同仁,大家下午好!很荣幸能够代表我们公司来这儿跟大家分享一下我们在电池检测这块所做的一些工作。
第一个环节,我想先介绍一下我们公司,普瑞赛思是一家第三方的检测机构,过去几年内主要专注于电池的检测,包括动力电池、储能电池还有消费类电池的检测与认证,我们也有一些新能源汽车核心零部件,比如充电桩、电机控制系统的检测,也有一些电池的分析工作。
接下来进入今天的正题,主要分三部分:储能系统安全风险分析、储能电池安全评估评价和检验项目、结论。
第一部分,这是一个完整的储能系统,是来自于韩国的储能系统,主要包括电池系统、控制系统,还有消防的,还有逆变器系统。具体失效的可能性,比如电芯环节可能会失效。电芯在使用过程中会老化,制造过程中会有一些制造的缺陷,有可能电芯在充放电过程中会膨胀,挤压这个模组其他的电池。还有外壳的密封失效,也包括电池泄露,也有一些绝缘情况。连接失效、连接松脱时,可能会有一些异常的高温情况。电池力阻的增大,电池管理系统的失效,这个可能更严重,比如对电池SOC的估计出现偏差,电池储能系统在运行过程中可能会有效率下降,严重SOC不准确有可能会作为电池的过充电或者过放电,有可能导致整个储能系统出现更为严重的灾害,会烧毁整个储能系统。
这是整个系统的风险点。具体到电池,在全生命周期内,电池有可能有其他几种模式,比如过充或者过放,制造缺陷引起的内部短路,在使用过程中有一些正负极短路和外部短路情况,还有电池的保护装置失效。同时,在实际运行过程中储能电站可能在高温环境重运行,也可能在低温环境中运行。供应商提供电池时都会给到一个具体的温度范围,比如零下20度到45度,如果超出这个范围锂电池可能会出现一些异常情况。比如低温下充电可能造成电池内短路。这都是比较严重的情况。
下面这几个图片是一些具体的变形案例(见PPT),电池的保护装置坏掉了,中间这个图下面是因为电池内短路造成电压有波动,不是一个稳定的状态,有可能会在正负10mV之内波动。
二、储能电池安全测试评价和验证项目。
这是目前我收集到的部分对电池尤其是储能系统的标准,其中包括我国的GB/T 36276,还有UL9540,还有UL9540A,9540A是针对电池热安全情况的标准,还有不是具有很针对性的,比如62619等都是针对电池的标准,但在储能系统中也是适用的。
这是目前整个标准所涵盖的要对电池进行检测的具体检测项目。主要分四个大类:寿命评价,这包括高低温性能、循环性能、存储性能、环境测试,涉及到实际在储能系统运行工况中的环境,比如在高海拔地方可能会有低气压的环境验证,海边可能有盐雾的验证,还有机械测试,比如振动测试,机械冲击,这可能在储能系统中去检测振动的不是太多,但在动力电池系统会检测振动,会检测机械冲击还有一些安全的测试项目,这是今天主要分享的内容。比如包括电极安全、机械安全、热安全,过充、过放、挤压、温度测试等。
除了测试项目外,还有对电池安全性能的评价,这个评价不只是为了确定这个电池是不是符合标准。这只是目的之一,但热失控安全的评价主要是探索这个厂家的电芯在什么样的情况下有可能会发生热失控,边界条件在哪里。比如它在短路,5毫欧和10毫欧有什么区别,性能55度和45度工作性能又有什么区别。主要是从材料性能开始到整个电芯的性能,进行一个安全边界的探索工作。
各位可能关心的更重要的是验证的项目,能不能通过GB/T 36276或者能不能通过9540A或者62610。这些都是验证的项目,直接给出一个测试的结果,这个电池符不符合标准,符合标准就给你通过的资质,不通过就要回去进行整改,但整改的方向要通过前面热安全评价部分确认。因为只有你非常了解这个电池的各项参数后才能对电池的设计进行优化。在储能系统的设计中也有这种情况,只有了解之后才能设计储能系统的BMS,才能优化储能系统运行的工况,根据实际运行的工况不断进行调整,保证这个电池在安全的区间内进行的工作。
这是第一个要分享的案例,外短路的测试,上面两个列出了UL1973和GB/T 36276测试标准和判定方法,最主要的差别就是短路电阻,36276里是5毫欧,1973里是20毫欧,这两个是有差别的。
左边是新鲜电池的短路测试,右边是老化之后容量衰减了50%左右。做这个项目是因为我们承接了南网科技部的一个项目,我们在里面承担了一部分工作,去验证老化之后电池的安全性,我们现在有一个梯次利用的场景。
新鲜电池在发生外部短路时,短路电阻36276的标准是5毫欧。在新电池发生短路时在安全区间内。下面T1、T2、T3、T4、T5是我们布在电芯不同地方的目的。整个温度是保持在50度以下的。即使发生了短路,情况是没有那么明显的。但对于老化之后的电池,在老化之后短路电阻瞬间下降的产热。比较高的绿线是我们布置的传感器(见PPT),就是探测电池有没有漏液。可以看到在短路发生后电池发生漏夜,在漏液的瞬间因为高温整个电池出现了热失控的情况,温度就升得比较高。
这个短路电阻的影响在这个PPT里看得比较清楚,我们是对同样两个模组,一个进行10毫欧的外短路,另外一个进行94毫欧的外短路。但给出来截然不同的两种结果。在10毫欧短路时,因为短路电流比较大,就会触发整个模组保护板的保护,后面电路断开之后没有持续的电流,整个模组在一个安全范围内,但94毫欧外短路时,因为电阻相当于升高了,电流比较小,导致保护电路没有及时启动,造成保护板有烧毁情况。这个情况在单体电池里也会有发现,比如对单体电芯来说1毫欧的短路和20毫欧的短路结果也不一样。因为1毫欧的短路,短路电流很大,很快会熔断,不会有其他的异常升温,但20毫欧货样更大的短路时,会持续对电池升温,有一个加热的过程,造成后来有热失控的发生,因为电池不断有加热过程。对电池的加热是造成电池失效一个很大的比例。
这是另外一个在储能系统应用场景下的非均衡充电情况(见PPT)。我们用了三个模组,模组一和模组二都是90%的SOC,就是为了验证这样一个工况。比如中间的模组坏掉了,要进行替换,但替换过去的模组有可能跟原始模组的SOC不一样。
比如一个系统的SOC是90%,但你换上去的可能是30%,也可能整个系统是30%,但换进去是100%的。这样就会造成换进去的模组有不均衡充电或者放电的过程。上面三幅图是100Ah放电的情况,整个模组的SOC尤其是模组三,有一个短暂的上升,但后面还会有持平。后面也验证了150Ah的电流,但限定电流可能只有30Ah,后面两个模组就没有办法充电或者放电了,因为模组之间有一个保护。但这个是在储能系统后面运维的情况需要考虑的非均衡充电或者非均衡放电的情况。这是比较正常的一种状况,在非均衡充电或者放电时是没有安全事故的。但有可能有些情况,比如你整个系统的容量比较大,合上时有拉弧或者持续加热的情况,也是需要我们去考虑的。
第三个案例是热失控测试。这是我们自己设计的防爆罐子,右边的曲线是一个电池我们对它进行加热热失控了,黄色和灰线是在电池两侧分别布置两个加热板进行加热,棕红色线是电池实际变化的曲线,前面因为温度比较低,在拐点之前是60度,保持得比较一致,但后面加热可以看到蓝线是电压的线,电压在突然下降那一瞬间电池已经开启了安全阀开启动作。在这之前我们没有停止加热,但看到加热功率还是一样的,黄色的线已经向上翘了。意味着电池发生开口之后已经导热了,导致整个加热板的温度已经远远高于我们给定的功率,电池已经发生了不可控的热失控。
这就会造成后面整个电池的燃烧,这个热失控有可能会进行扩散。为什么要在罐子里做测试?因为我们还要分析热失控之后的气体。这是热失控后的气体情况(见PPT)。比如三元电池是左边两幅图,磷酸铁锂是右边两幅图,三元电池和磷酸铁锂在加热时产生的气体也不一样。对于产品气体的体积进行归一化处理时,右边的表格里三元电池在加热时产生的气体体积在25度时每Ah可能要产生3升的前提,但铁锂来说每Ah可能产生8-9升的气体。这也是需要考虑的,因为产生了这些气体,图表中的一些成分,比如有一氧化碳或者烷烃、烯烃类气体都是可燃的,有些也是有毒的气体。我们在设计时可能也可以用这些气体做一个传感的信号,也可以通过这些气体的检测来对储能系统后面的预警或者消防做相应的改善。
热失控扩散,我们调查了热失控扩散的路径,同样12颗电芯做成的不同路径,有串联和并联的,但对于整个热失控的扩展来说,没有特别大的区别,热失控热量在第一颗电芯发生热失控后,热量通过电池的大面传递到第二颗电池,最终造成整个电池的热失控。这是因为中间没有有效的隔热系统或者阻燃系统,如果在里面加入了有效的隔热系统或者阻燃系统,扩展速度有可能会降低或者不会扩展,因为在热失控发生的初期,如果电池的散热速度要大于产热速度,有可能这些热失控在最开始就会被抑制掉。
这是我们研究热失控扩展过程中电芯的影响,一个是53Ah的电芯,一个是37Ah的电芯,两个电芯表现初步统的热失控情况。比如53Ah的在200度范围内没有发生热失控。但37Ah的电芯在120度左右电池会压开阀。我们做热失控测试时有这样的情况,因为加热时采取单面加热和双面加热,对电池加热的功率是不一样的。在加热过程中造成电池热失控的最主要原因是在加热到特定温度,比如130度,有可能你的隔膜会溃缩,正负极之间接触,造成电池短路产热,最终导致电池产生一个热失控。37Ah时的电芯为什么会在120度开启,可能有一部分原因是因为这个电池相对比较小,电池外部的热量向内传递时速度要快一些。这个验证工作我们也在接着分析材料方面的影响。
另外一块分享一下热失控扩展,我们会对整个电池包的热失控扩展,我们会对电池包其中某一颗电芯做一个热失控,比如加热触发热失控,看热失控在整个电池系统中扩展的情况。目标电芯在2-3分钟后电池箱内的安全阀开启了,对于储能系统来说储能柜大一点有可能开启得更晚。热失控电芯在高温下会产生大量气体,在安全阀开机之后会喷出来大量的气体。这个气体就是一个高温的气体,会在你电池箱的内部聚集,会加热其他的电池,导致最终电池出现一个热失控的情况。如果第一颗电芯出现了热失控,第一颗电芯和第二颗电芯之间热失控的时间要远远大于第二颗电芯和第三颗电芯热失控的时间间隔。这时候电池箱内整个温度已经很高了,会对电池箱内的其他单体电芯加热失控造成更多电池开阀,会有更多的高温气体在电池箱内累计,会造成加速热失控扩展的情况。比较严重的情况是烧到最后的,这可能在新能源汽车的各种新闻报道中也看到,有些电池箱爆炸的就是因为电池箱内的可燃气体累计在内,会造成电池箱的热失控。
这是我们GB/T 36276里特别强调的测试,绝热温升测试,研究电池在加热情况下的热反应,去探索热安全的边界。比如热失控发生的起点在哪里,中间会有一个什么样的情况,可以从右边的图看到,红色的是在绝热环境下,蓝色在正常环境下。在绝热环境下热失控拐点发生后,产热功率远远高过正常情况下的产热功率。因为绝热情况下没有散热,导致整个热量在内部累计,会计算出一个产热功率明显增大。
电池的安全是系统性的,有多种因素会影响整个电池的安全性能,即使采用安全的电芯,最后也有可能由于工程设计的不合理造成电池在不合理的区间运行,产生一个安全的风险。也没有绝对安全的电池化学体系,无论是三元还是铁锂还是钛酸锂,没有绝对安全的,都有一定可能性会发生热失控,我们可以通过选择热稳定性高的电芯和优化电池设计来减少热失控扩散的过程,最后需要特别强调的是为保证电池系统的合理性和安全性,做系统设计的也需要知道电芯的安全边界,来优化BMS或者优化整个储能系统的设计。
我们公司在过去几年内一直做储能电池,国内一些主流的电池厂商还有国际上的一些新能源汽车厂商都是我们的合作伙伴,也都在我们那儿进行了大量测试,欢迎有测试需求的跟我交流联系,谢谢大家!