近日,宝钛股份与国家电投成功签订“国家示范城市联合申报企业合作意向书”项目及首批钛材料采购合同,标志着宝钛股份进入新的钛材应用领域。

该项目积极推动京津冀、湖北、浙江等地区燃料电池汽车产业示范城市群的建设,对实现相关基础材料、关键零部件研发,以及国家燃料电池汽车行业的发展提供了核心技术支持。
早在2017年,宝钛股份就已提前布局,宝钛研究院及相关单位成立了氢能项目组,根据国家战略以及未来市场需求,开始研发氢燃料电池用钛的技术攻关工作 。在这期间,宝钛项目组紧紧围绕氢燃料电池金属双极板性能的要求,积极主动攻坚克难、反复试验。2019年10月,钛金属双极板 在第一台新能源氢能巴士上成功应用,经后期测试完全满足前期设计要求。2020年9月27日,氢燃料电池产品发布会在宁波召开,宝钛应邀参会并迎来了新的发展机遇。
关于钛双极板
钛及钛合金 密度低、比强度高且在酸性环境中耐蚀性优异,在氢燃料电池双极板中具有较高的应用价值。
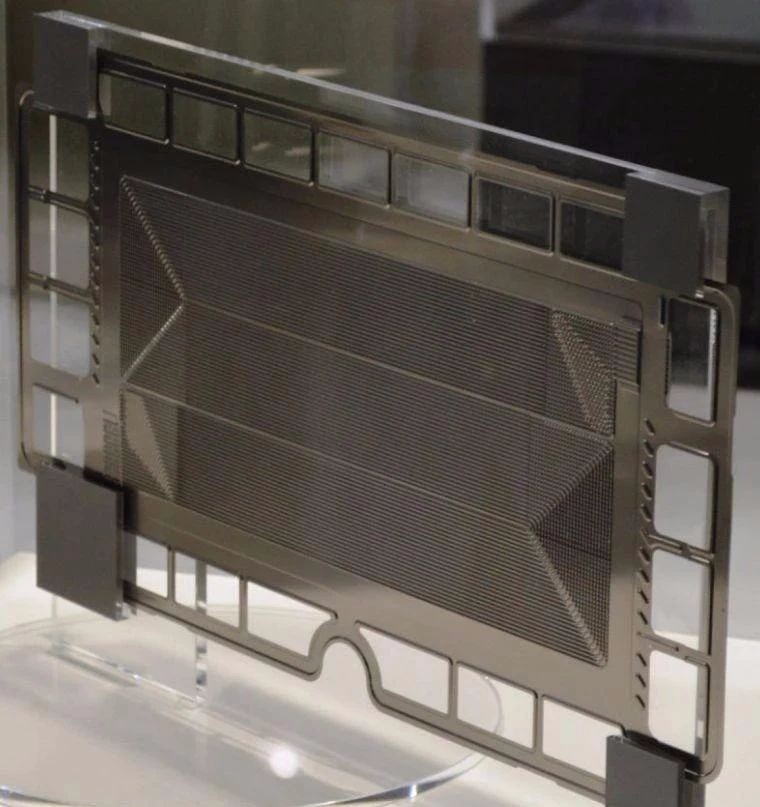
双极板作为PEMFC的重要组成部分,占电堆重量的 70% 以上,体积的 50% 左右,其成本为电池成本的 30% ~ 50% 左右。双极板材料主要分为 3 类,分别为石墨双极板 、复合材料双极板 、金属双极板 。
其中,石墨双极板重量轻、耐蚀性好、导电导热性能优异,但脆性大,流场加工成本高; 复合材料双极板成形性能优异、机械强度高,但导电性较差,且加工成本较高; 相比之下金属双极板厚度薄、导电导热性能优异、机械强度高且气体隔绝性好,有利于电池比功率密度的提升,此外金属材料加工工艺成熟,可利用冲压、压铸和激光成形等方式加工高精度的复杂流场,容易实现极板的量化生产,已成为氢燃料电池的主流双极板材料。
金属双极板材料一般分为不锈钢 、铝合金 、钛合金 ,其中钛在 PEMFC 环境中的耐蚀性能优于不锈钢和铝合金,且其比强度高,能够进一步降低极板的重量,提高 PEMFC 的比功率密度。 如日本丰田MIRAI燃料电池汽车选用钛作为双极板材料,并采用 3D 网状流场结构设计,相较于不锈钢直流道流场双极板,其电堆质量功率密度和体积功率密度有了大幅提升。
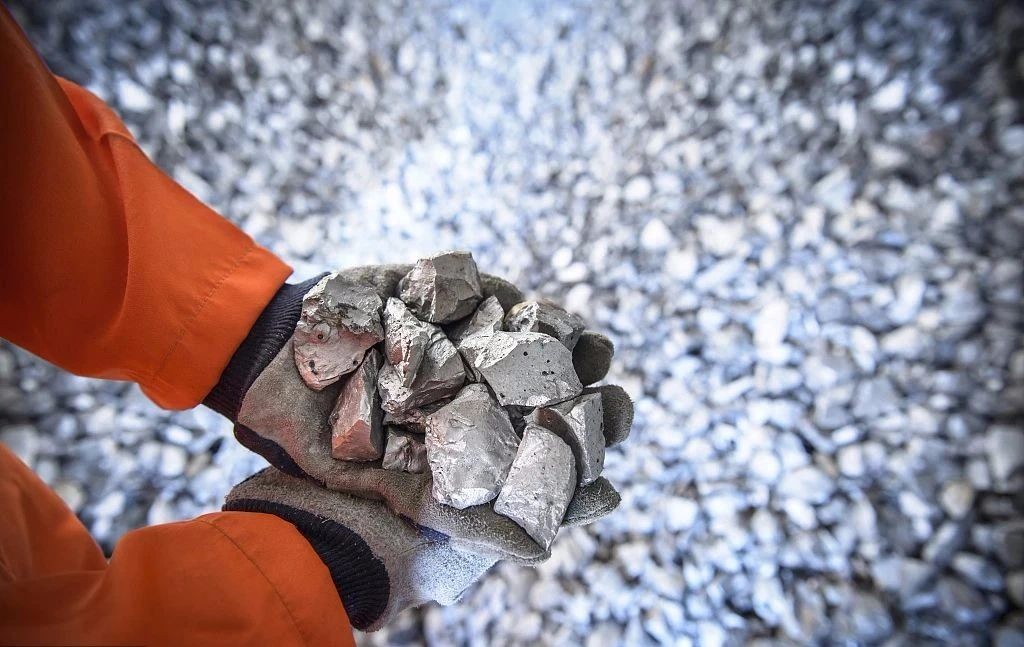
当前制约氢燃料电池商业化推广的两个重要问题是成本 和耐久性 ,而极板材料、流场加工及极板涂层制备工艺一定程度上决定了双极板的成本。
石墨和碳基复合材料在性能上已经不能满足氢燃料电池的要求,金属材料现已成为氢燃料电池双极板的主流材料。 此外,高功率一直是氢燃料电池的追求目标,金属材料中钛及钛合金密度低、比强度高,在氢燃料电池中具有优良的耐蚀性,可以明显降低双极板重量和体积,从而显著提升电池的质量比功率和体积比功率,且钛及钛合金在长期服役运行过程中产生的腐蚀产物对质子交换模和催化剂的毒性较弱,有利于提升电池运行的稳定性和耐久性。
钛双极板表面制备的金属碳/氮化物和无定型碳涂层综合性能优越,具有较高的研究和应用价值,然而这些涂层易出现针孔缺陷等,因此目前研究的主要目标是提升涂层致密性、膜基结合强度和涂层表面导电性。此外涂层还应具有良好疏水性,以促进反应生成水的排出。要满足这些综合性能,对涂层的结构设计和组织成分提出了更高要求。
涂层结构组织的复合化和纳米化可以一定程度提升涂层致密性、耐蚀性、导电性,增强钛极板服役稳定性和可靠性,是今后发展的主要方向。