关键词:关键焊接难题 科技创新 技术升级 高质量发展
背景PART 01
机械科学研究总院集团有限公司是国务院国资委直接监管的公益类中央大型科技企业集团,始建于1956年。六十余年来,集团始终坚守“提升中国装备制造水平”的初心使命,持续深耕装备制造业基础共性技术研究,创造了200多项全国工业领域的第一,累计取得7000多项科研成果,广泛应用于机械制造、汽车、航空航天、环保、能源、交通运输、信息产业、冶金、化工、建筑等国民经济和国防安全重要产业领域,为我国重大科技项目攻关、重大工程建设、行业共性关键技术发展做出了巨大贡献。
集团目前拥有19家全资及控股子企业(公司),建有1个国家制造业创新中心、4个国家重点实验室、4个国家工程研究中心,集科研开发、科技产业和技术服务三大业务功能为一体,是国家科技创新体系的重要组成部分和装备制造业发展的重要引擎。
责任行动PART 02
(一)取得4项科技创新 技术成果整体达世界先进水平
在国际科技合作专项、哈尔滨市科技攻关计划等项目的支持下,机械总院集团哈焊院历经二十年系统研究了激光及激光电弧复合应用理论基础、核心工艺、关键共性工程技术、成套装备和标准体系等制约技术发展的关键卡脖子问题,取得了4项科技创新:
首次提出了“双重导电”、“电弧辐射增强”机制和“电弧等效功率”热源匹配模型,揭示了激光-电弧复合焊接物理作用机制。
攻克了25米大型薄壁铝合金型材连续稳定焊接、复杂工况单面焊双面成形闭环控制、多层多道焊智能排序等关键工程技术难题,开发了具有自主知识产权的形性可靠调控系列化激光及激光-电弧复合焊接新工艺。
攻克了焊接过程在线检测、多轴协调及精度补偿、工况闭环控制等关键技术,研制出5大类、10余种系列化成套国产激光及激光-电弧复合焊接系统。
形成了较为完整的激光及激光-电弧复合焊接制造国家标准体系。
鉴定专家认为,本项目技术成果整体水平达到了国际先进水平,部分成果国际领先,在部分领域已实现了进口替代。
(二)成功解决大吨位全路面汽车起重机伸臂焊接工艺难题
大吨位全路面汽车起重机通常是指吊装能力大于100吨的产品,当前已经投放市场的最大吨位的全路面汽车起重机为1200吨。伸臂是全路面汽车起重机的关键部件,每台起重机通常有5-8节伸臂。伸臂的原有焊接工艺采用了“单丝MAG手工焊打底+双丝MAG焊填充”的弧焊工艺,存在的问题主要有:采用自动化或机械化弧焊工艺无法实现伸臂的单面焊双面成形焊接,必须依靠手工焊进行打底焊。而手工打底焊劳动强度大,操作环境恶劣,焊缝质量的可靠稳定性差。焊接变形大,且焊接变形无规律,焊后校形处理工作量大、难度大。
针对全路面汽车起重机伸臂原有弧焊工艺存在的技术问题,机械总院集团设计开发了我国第一套在焊接生产线上应用的大功率固体激光-熔化极电弧复合热源焊接专机,并成功地应用于了伸臂的焊接生产,重点解决了原有弧焊工艺存在的关键技术问题。
项目投入使用后,累计焊接伸臂9000多根,装配1400多台大吨位起重机产品,焊缝累计长度超过300公里,为企业创造直接经济效益近8亿元,间接经济效益40多亿元,大幅度提升了我国工程机械装备的整体制造水平,引领了行业技术进步,为企业带来良好的经济效益和社会效益。技术成果曾获2018年中央电视台《中国财经报道——感受中国制造新高度》栏目报道。
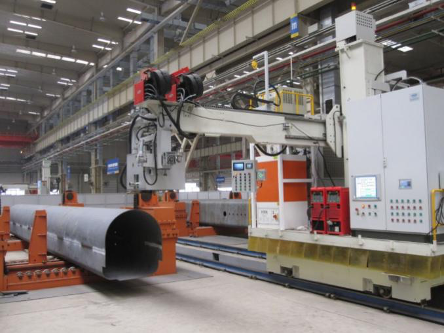
大吨位起重机伸臂激光-电弧复合焊接专机
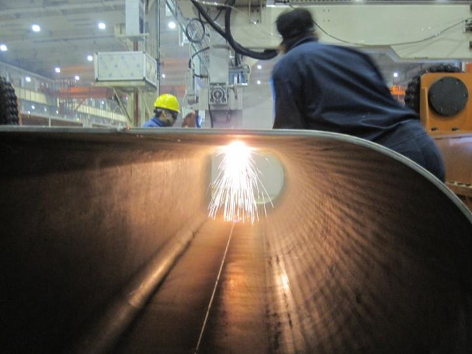
大吨位起重机伸臂复合焊接过程照片
(三)加速推进我国高速磁悬浮列车自主化与产业化进程
高速磁浮作为一种新型尖端轨道交通技术,是科技部“十三五”国家重点研发计划“先进轨道交通”重点专项的课题之一,其优势已被越来越多的国家关注。日本的超导磁浮技术实现603km/h的试验速度,德国的磁浮技术最高试验速度达到505km/h,而时速600公里高速磁浮系统及工程化应用在我国尚属空白。
铝合金车体作为600公里高速磁浮列车的关键部件,其结构特点、制造理念与传统动车组截然不同,具体体现在:
1、传统动车车体重量约为9吨,而磁浮车体重量要求小于6.7吨,构成车体的铝合金双层型材的壁厚和焊接厚度均减小,焊接变形控制难度大幅增大。
2、磁浮车体的制造精度公差进一步提高,仅为传统动车的1/2~1/4。磁浮车体制造要求焊后免调修,这与传统动车一般采用焊后机械+火焰调修方法有很大区别,这对焊接变形精度控制提出更高要求。
3、磁浮车体的强度指标高于传统动车,磁浮车体静强度安全系数大于1。
4、疲劳寿命按照气密强度满足±7000Pa、1000万次进行评估。这对焊接接头质量提出更高要求。
新的结构、制造精度和服役性能对车体部件焊接工艺及装备提出了新的要求和挑战。传统的工艺方法存在焊接变形大、接头强度弱化、生产效率低等关键工程问题,已无法满足新一代磁悬浮列车对车体部件高精度、高质量、高性能的苛刻要求。选择一种高效优质的先进焊接新工艺方法,通过系统研究及工程化验证,建立起完整的新型焊接制造工艺体系和质量评价体系,是解决上述高速磁浮列车车体制造关键问题最有效的、且唯一的途径。
机械总院集团哈焊院研发的激光-电弧复合焊接的主要技术优势恰好可以弥补传统弧焊和搅拌摩擦焊的不足,是解决新一代600km/h磁浮列车制造关键问题,确保实现车体部件轻量化、高精度、高可靠性制造的最佳工艺选择。项目的成功实施能够满足轨道交通领域新一代600km/h磁浮列车制造的迫切需求,促进我国高速磁悬浮列车完全自主化与产业化进程,也有利于提升我国高端激光加工成套工艺及装备的技术水平,为企业带来良好的社会效益和经济效益,项目意义重大。
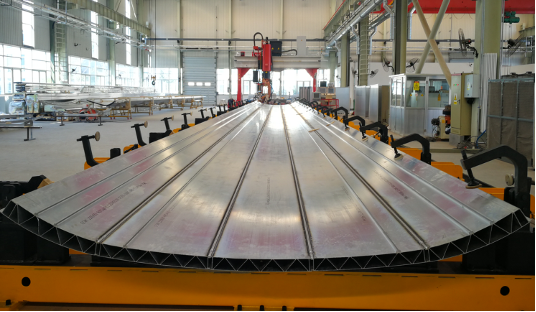
履责成效PART 03
机械总院集团哈焊院研发的激光及激光-电弧复合焊关键应用基础、工程技术与成套装备项目获得授权发明专利19件、实用新型专利4件、软件著作权1件;制定国际标准(CD阶段)1项、国家标准9项、行业标准1项。
技术成果已在军工、工程机械、轨道交通、石化、煤炭机械、造船等领域获得了较为广泛的应用,累计销售各类激光焊接装备23台套,完成9000多根起大型重机伸臂焊接(焊缝总长度超过300km),焊接各种轨道车辆3443辆,累计销售收入超77亿元,创外汇19亿美元。该成果获得2019年度中国机械工业科学技术奖一等奖。
展望PART 04
面向未来,机械总院集团将坚持以提升中国装备制造水平为己任,不忘初心,牢记使命,推进实施创新驱动发展战略,聚焦国家战略、行业急需“卡脖子”、“短板”技术方向,瞄准先进制造中的高端材料、共性技术及装备,积极打造面向行业技术进步的创新平台、面向产业发展的服务平台和面向国家重大工程的支撑平台,致力于成为行业科技创新领跑者、重大工程支撑者、科技产业主力军,努力打造“百年科技研发集团”,坚定履行公益类科技型中央企业的政治责任、经济责任和社会责任,为建设现代化制造强国、实现伟大复兴中国梦做出新的更大贡献!