6月19日,位于秦皇岛经济技术开发区东区的哈电集团(秦皇岛)重型装备有限公司(以下简称“哈电重装”)核岛厂房里,一台长约21米、重达370吨的“大家伙”被缓缓吊起,运至厂房外码头的货船上,从当天起,此批共3台“华龙一号”ZH-65型蒸汽发生器将陆续发往漳州核电厂。
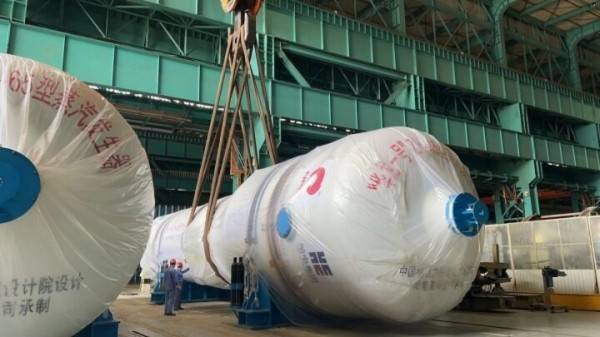
生产制造部项目计调员陈哲介绍,核电蒸汽发生器是压水堆核电厂反应堆冷却剂系统的核心设备之一,在运行过程中承担着产汽、放射性包容、导出堆芯余热的重要功能,简单些说,蒸汽发生器就是将核电站堆芯产生的热量转化为蒸汽用于发电。
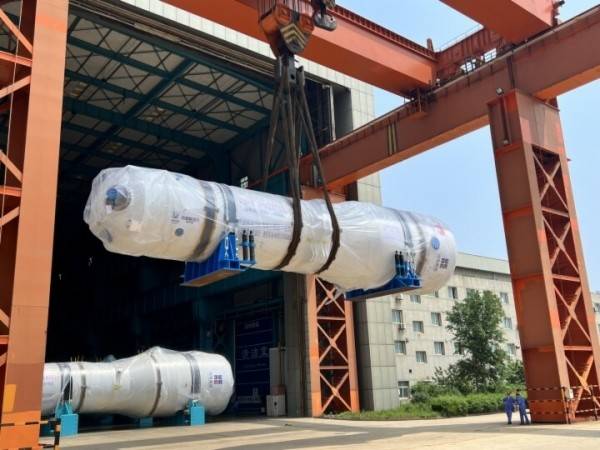
“华龙一号”ZH-65型蒸汽发生器(以下简称“华龙一号”)是完全由我国自主研发制造、具有独立自主知识产权的第三代核电蒸汽发生器。与国外同类产品相比,“华龙一号”出口蒸汽湿度更低、出口饱和蒸汽压力更高、功率重量比更高,设计使用寿命达到60年,比国外产品多了20年。此外,“华龙一号”采用了国际最高安全标准,陈哲说:“比如,相比国外同类产品,‘华龙一号’增加了很多检测检验设备,另外,即使发生停电事故,也可以自动启动安全系统,稳定性、安全性更可靠,符合我国‘安全第一’的核电理念。”
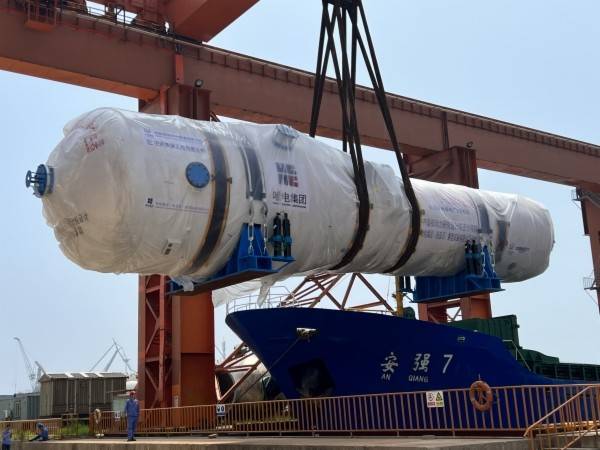
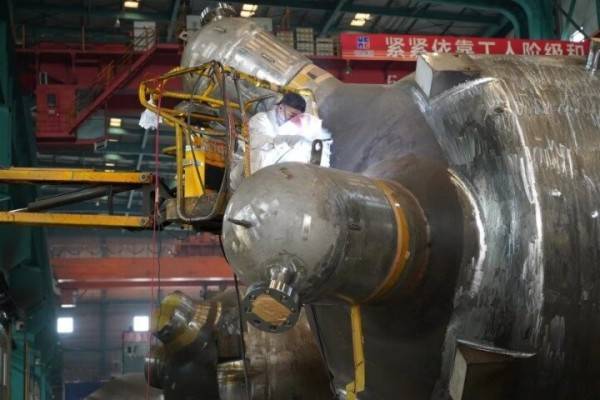
“华龙一号”制造工艺对技术要求极高,作为制造单位,哈电重装在生产过程中面临着一个又一个技术上的挑战。以深孔钻打孔技术来说,在一个管板上要打11670个孔,每个孔与其他孔的间距要保持一致,每一个孔径精确到0.01毫米,垂直度和粗糙度要求非常高。工程师和工人为此一遍遍做实验,选择最适合的工具、最稳妥的技术,攻克了这一技术难关。再比如换热管焊接技术,关系到核辐射水安全问题,必须保证无损检测合格,因此对焊接技术要求非常高,也是在一次次实验中,工程师和工人搜集统计焊接电流、钨极、间隙等各种数据,找到最好的一个焊接的点。在蒸汽发生器内部有5835根镍基合金倒U型传热管,它们几乎没有一根完全相同,为了保证焊接质量,哈电重装自主研发的管子管板镍基合金焊接等关键技术又一次解决这个技术难题。《华龙一号ZH-65型蒸汽发生器关键工艺研究》顺利通过核能行业协会鉴定,荣获中国核能行业协会科技进步奖二等奖,产品也被列入河北省制造业单项冠军产品名单。

从2018年开始,哈电重装进行“华龙一号”蒸汽发生器的批量化生产,为福建漳州等地3个核电厂的4个机组生产制造共12台蒸汽发生器。漳州核电1号机组三台蒸汽发生器已于2021年8月交货,2号机组的三台也已通过了由中国核动力研究设计院、中核国电漳州能源有限公司联合组成的验收组的出厂验收,具备了交货条件,陆续发往漳州核电厂。